Health Surveillance
Health surveillance is the process of monitoring the health of employees exposed to specific health risks during the course of their work. Employers need to provide surveillance to demonstrate that they are meeting their duty of care for their employees.
Section 2 of the Health and Safety at Work Act 1974 (HSWA) states that employers have a general duty of care to ensure, so far as is reasonably practicable, the health, safety and welfare of all their employees. Health surveillance is about having procedures in place to detect work-related ill-health at an early stage and acting on the results (HSE, 2005).
Employers have a duty to reduce, so far as is reasonably practicable, the risks to the health and safety of employees and others who may be affected by work activity. The employer needs to identify hazards and assess the risks. Adequate risk assessment will identify significant residual risk to health even after reasonably practicable control measures have been applied. Employees need to understand their role and responsibilities for health and safety; this includes their responsibilities within a health surveillance programme.
Occupational health focuses on the protection and promotion of the health of workers by preventing and controlling occupational diseases and accidents. The aim is to eliminate occupational factors and conditions hazardous to health and safety at work. A suitable health surveillance programme aims to prevent ill health rather than cure it.
Our Health Surveillance Services
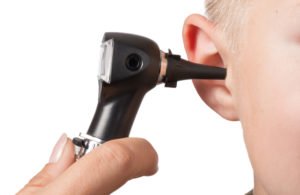
Audiometry
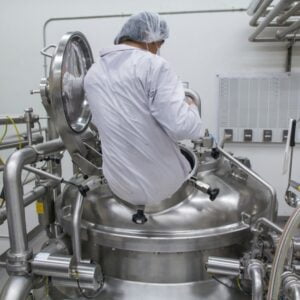
Confined Space Medical
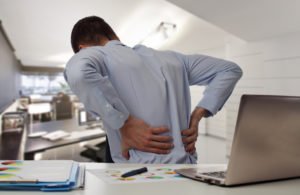
Display Screen Equipment (DSE)
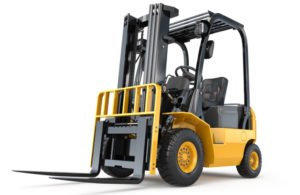
Forklift, Mobile Plant and Company Driver Medicals
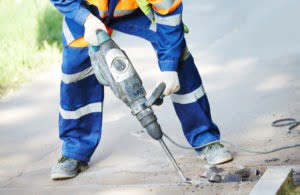
Hand-Arm Vibration Tier 1 – Tier 4
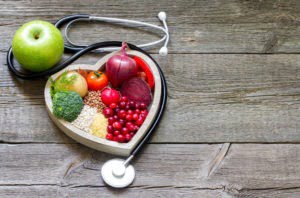
Healthy Worker Medicals
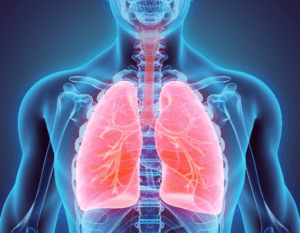
Lung Function (Spirometry)

Musculoskeletal Assessment
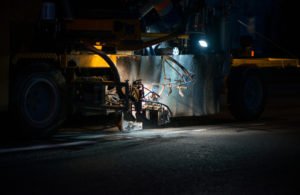
Night Shift Workers
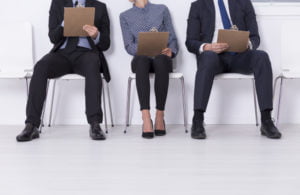
Post Offer Medical
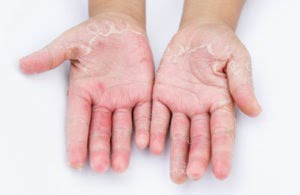
Skin (Dermatology)
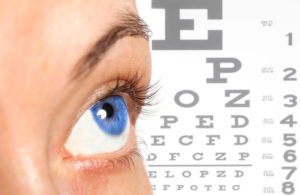
Vision Testing
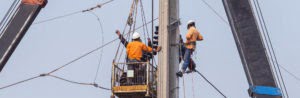
Working at Height Medical
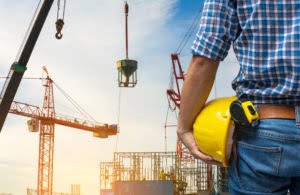