Hand-Arm Vibration Syndrome (HAVS) is a serious and debilitating condition that affects workers using hand-held power tools and machinery that transmit vibration. This syndrome can lead to significant health issues, including damage to blood vessels, nerves, and joints of the hand, wrist, and arm. Consequently, HAVS is recognised as a significant occupational health risk, prompting the implementation of stringent regulations to protect workers from its harmful effects. Employers, therefore, have a legal obligation to safeguard their employees from excessive vibration exposure. Understanding and complying with HAVS regulations is crucial for maintaining workplace safety and health standards.
Whether you are an employer, manager, or health and safety officer, read on for an in-depth look at what exactly HAVS is. We’ll explain the relevant regulations and how to effectively implement and adhere to them in the workplace
In This Article:
What Is HAVS?
1) Definition of HAVS
Hand-Arm Vibration Syndrome (HAVS) is a medical condition caused by prolonged and repeated exposure to hand-arm vibration, typically from the use of hand-held power tools and machinery. The syndrome encompasses a range of disorders that affect the blood vessels, nerves, muscles, and joints of the hand, wrist, and arm. HAVS is recognised as a serious occupational illness and is preventable with proper measures in place.
2) Causes of HAVS
The primary cause of HAVS is prolonged and repeated exposure to hand-arm vibration. This exposure typically comes from the use of tools and machinery that transmit vibrations into the hands and arms. Common sources include:
- Power Tools: Such as drills, grinders, sanders, and chainsaws.
- Machinery: Such as jackhammers, pneumatic tools, and vibrating compaction equipment.
- Industrial Equipment: Including assembly line tools and heavy-duty mechanical equipment.
The vibrations from these tools can damage the small blood vessels and nerves in the hands and arms, leading to HAVS over time.
3) Symptoms of HAVS
The symptoms of HAVS can vary but often develop gradually and worsen with continued exposure. Common symptoms include:
- Tingling and Numbness: Often in the fingers, which can become permanent if exposure continues.
- Loss of Strength: Grip strength may decline, making it difficult to hold or manipulate objects.
- White Finger (Raynaud’s Phenomenon): This is a blanching of the fingers, usually comes on in cold or damp conditions, where fingers turn white and feel cold and numb.
- Pain and Discomfort: In the hands and arms, which can be constant or intermittent.
- Reduced Dexterity: Difficulty with fine motor tasks due to loss of coordination and sensation.
Early detection and intervention are crucial to prevent permanent damage and manage the symptoms effectively. Regular monitoring and adhering to safety regulations can help mitigate the risks associated with HAVS.
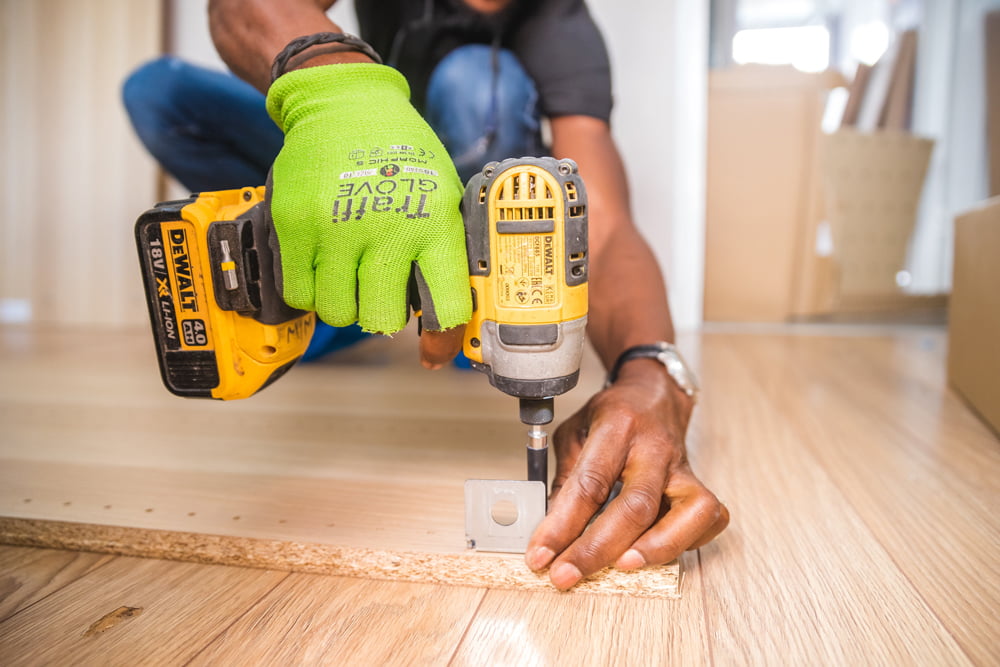
Key HAVS Regulations
Firstly, employers must conduct thorough risk assessments to identify and evaluate vibration hazards in the workplace. This step is crucial in understanding the extent of exposure and the necessary measures to mitigate risks.
Secondly, control measures must be implemented to eliminate or reduce exposure to vibration. These measures can include modifying work practices, using alternative tools, and providing personal protective equipment (PPE).
Moreover, employers are required to inform and train employees about the risks of vibration. This includes educating them on safe work practices and proper usage of tools and equipment to minimize exposure.
Lastly, regular health surveillance is essential. Workers who are at risk of HAVS should undergo regular health checks to detect early signs of the syndrome and take preventive action. This proactive approach ensures that health issues are identified and addressed promptly.
The regulations set specific limits for vibration exposure to protect workers:
- Exposure Action Value (EAV): The EAV is a daily amount of vibration exposure above which employers must take action to control exposure. For hand-arm vibration, the EAV is 2.5 m/s² A(8). When this level is reached or exceeded, employers must implement measures to reduce exposure and provide health surveillance.
- Exposure Limit Value (ELV): The ELV is the maximum amount of vibration exposure an employee can be exposed to in a single day. For hand-arm vibration, the ELV is 5.0 m/s² A(8). Employers must ensure that no employee exceeds this level of exposure on any single day.
These values are critical in ensuring that workers’ exposure to vibration is within safe limits, thus reducing the risk of developing HAVS.
3) Risk Assessment Requirements
Conducting risk assessments is a fundamental requirement under the Control of Vibration at Work Regulations 2005. The process involves:
- Identifying Vibration Hazards: Recognise sources of hand-arm vibration in the workplace, such as specific tools and machinery.
- Measuring Vibration Levels: Use appropriate methods to measure the vibration levels produced by these tools and machinery.
- Evaluating Exposure: Calculate daily vibration exposure for workers based on the duration and intensity of exposure.
- Implementing Control Measures: Develop and implement strategies to reduce or eliminate exposure to vibration, such as using anti-vibration tools, altering work practices, or providing PPE.
- Monitoring and Reviewing: Regularly review the effectiveness of control measures and make adjustments as necessary to ensure ongoing protection for workers.
By adhering to these regulations and maintaining vigilance through regular risk assessments and health surveillance, employers can significantly reduce the risks associated with hand-arm vibration and protect their workers’ health and safety.
Employer Responsibilities
1) Implementing Controls
Employers must implement effective control measures to reduce vibration exposure in the workplace. Here are key steps to take:
- Tool Maintenance: Ensuring tools and machinery are well-maintained is crucial. This includes sharpening blades, balancing rotating parts, and replacing worn-out components. Well-maintained equipment produces less vibration, thereby reducing the risk to workers.
- Job Rotation: To minimise prolonged exposure, employers can rotate employees through different tasks. This strategy ensures that no single worker endures high levels of vibration for extended periods.
- Use of Anti-Vibration Tools: Providing anti-vibration tools and equipment is essential. These tools produce lower levels of vibration, thereby reducing the risk of HAVS.
- Work Practices: Modifying work practices can further minimise vibration exposure. This could involve altering certain tasks, using damping techniques, or reducing the time workers spend on high-vibration tasks.
- Vibration Dampening Materials: Installing vibration-dampening materials on work surfaces and handles can help absorb some of the vibrations, thus reducing the amount transferred to workers.
By incorporating these measures, employers can effectively reduce vibration exposure and protect their workers from the harmful effects of HAVS.
2) Providing Training
Firstly, it’s essential to inform workers about the dangers of vibration exposure and the symptoms of HAVS. Raising awareness of these risks is the foundation of prevention.
Next, employees should learn the correct use of tools and machinery to minimise vibration exposure. This training includes demonstrating proper grip techniques and emphasizing the importance of taking regular breaks to reduce cumulative exposure.
Additionally, instruct workers on how to properly maintain their tools to keep vibration levels low. Regular maintenance practices can significantly reduce the risks associated with vibration.
Finally, encourage employees to report any symptoms of HAVS early. They should understand the procedures for reporting these symptoms to ensure timely intervention and prevent further harm.
3) Health Surveillance
Regular health checks and monitoring are essential for workers exposed to vibration. This includes:
- Baseline Health Assessments: Conduct initial health assessments for all employees exposed to vibration to establish a baseline of their health.
- Regular Monitoring: Implement periodic health checks to monitor any changes in workers’ health. This helps in the early detection of HAVS symptoms and ensures timely intervention.
- Recording and Action: Maintain accurate health records for all employees exposed to vibration. If symptoms of HAVS emerge, employers must take appropriate action, which could include modifying work practices, rotating job roles, or even temporarily removing the affected worker from high-vibration tasks.
- Access to Medical Advice: Provide employees with access to occupational health professionals who can offer advice and treatment if symptoms of HAVS are detected.
By taking these responsibilities seriously and implementing comprehensive control measures, training, and health surveillance, employers can significantly reduce the risks associated with vibration exposure and protect the health and well-being of their workers.
Employee Responsibilities
1) Proper Tool Use
Employees play a crucial role in preventing Hand-Arm Vibration Syndrome (HAVS) by using tools correctly and adhering to safety guidelines. Key responsibilities include:
- Following Manufacturer Instructions: Employees should always use tools and machinery according to the manufacturer’s instructions. This ensures that the equipment is used safely and effectively, minimising the risk of excessive vibration.
- Using Tools Properly: Proper tool use is essential to reduce vibration exposure. Employees should be trained to grip tools correctly, avoid excessive force, and use tools designed for the specific task at hand.
- Maintaining Tools: Workers should ensure that tools are well-maintained and report any signs of wear or damage to their supervisors. Proper maintenance, such as sharpening blades and balancing rotating parts, can significantly reduce vibration levels.
- Taking Regular Breaks: It is important for employees to take regular breaks from tasks that involve high levels of vibration. This helps to reduce the cumulative exposure to vibration throughout the workday.
- Using Personal Protective Equipment (PPE): When appropriate, employees should use anti-vibration gloves and other PPE designed to reduce the transmission of vibrations to the hands and arms.
2) Reporting Symptoms
Early detection and reporting of HAVS symptoms are vital for effective treatment and prevention of further damage. You should encourage employees to:
- Monitor Symptoms: Be aware of the symptoms of HAVS, such as tingling, numbness, or loss of strength in the hands and arms. Recognising these symptoms early can prevent the condition from worsening.
- Report Promptly: Report any symptoms of HAVS to their supervisor or occupational health professional immediately. Early reporting can lead to timely interventions, reducing the risk of permanent damage.
- Participate in Health Surveillance: Engage in regular health checks and monitoring provided by the employer. This helps to track any changes in health status and ensures early detection of HAVS symptoms.
- Follow Health Advice: Adhere to any health advice or treatment plans provided by medical professionals. This may include modifications to work practices, use of specific tools, or temporary reassignment to lower-vibration tasks.
By understanding and fulfilling their responsibilities, employees can contribute significantly to reducing the risk of HAVS and ensuring a safer working environment for everyone.
Preventative Measures
1) Engineering Controls
Implementing engineering controls is the most effective way to reduce exposure to hand-arm vibration. These controls involve modifying equipment and processes to lower vibration at the source.
Utilising tools designed to minimise vibration is essential. Anti-vibration tools, equipped with features that dampen vibrations, significantly reduce the amount transmitted to the hands and arms. These tools can greatly lower the risk of developing HAVS.
Regular maintenance of tools is also crucial. This includes keeping tools sharp, balanced, and properly lubricated. Additionally, upgrading to newer, low-vibration models can make a substantial difference in reducing exposure.
Another important measure is using tools with shock-absorbing handles, which can decrease the transmission of vibrations to the user. These handles are typically made from materials designed to dissipate vibration energy, further protecting workers from the harmful effects of vibration.
By incorporating these engineering solutions, employers can effectively reduce the risks associated with hand-arm vibration, thereby safeguarding their employees’ health and wellbeing.
2) Administrative Controls
Administrative controls involve changes to work practices and policies to reduce exposure to vibration. These strategies include:
- Limiting Exposure Time: Implementing work schedules that limit the time workers are exposed to vibrating tools can help reduce the risk of HAVS. This might involve rotating employees through different tasks or limiting the duration of exposure to vibrating equipment.
- Scheduling Regular Breaks: Ensuring that employees take regular breaks from using vibrating tools can help reduce the cumulative exposure to vibration. Breaks allow time for blood circulation to recover, reducing the risk of damage.
- Training and Education: Providing training on the proper use and maintenance of tools, as well as the risks of vibration exposure, is crucial. Educating employees about the symptoms of HAVS and the importance of early reporting can also help in early detection and prevention.
3) Personal Protective Equipment (PPE)
Personal protective equipment can provide an additional layer of protection against HAVS. While PPE should not be the sole method of control, it can be an effective supplement to engineering and administrative measures. Key PPE includes:
- Anti-Vibration Gloves: These gloves are designed to reduce the amount of vibration transmitted to the hands. They are made from materials that absorb and dissipate vibration energy. It’s important to select gloves that are suitable for the specific tools and tasks being performed.
- Hearing Protection: While primarily aimed at protecting hearing, ear protection can also serve as a reminder of the importance of overall occupational health and safety, including the prevention of HAVS.
- Warm Clothing: Cold temperatures can exacerbate the effects of vibration exposure. Ensuring that workers are adequately dressed for the environment can help maintain good circulation and reduce the risk of HAVS.
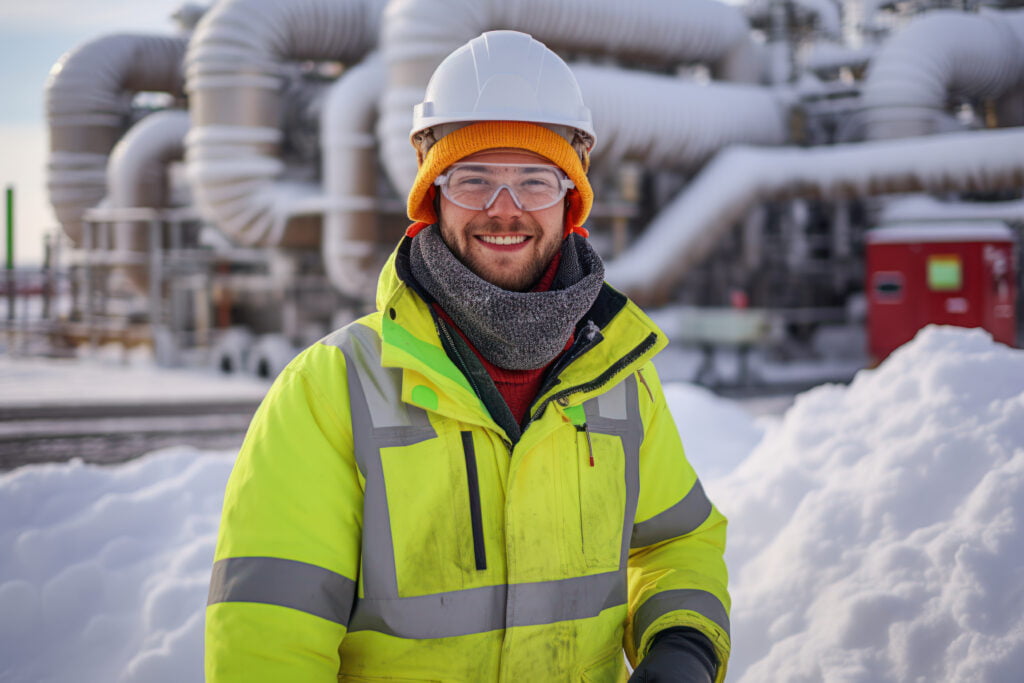
Monitoring and Health Surveillance for HAVS
1) Tier 1: Initial Health Assessment
Purpose: Establish a baseline for new employees who will be performing tasks involving hand-arm vibration.
Components:
- Questionnaire: Identifies any pre-existing symptoms or conditions.
- Medical History: Reviews the employee’s medical history, focusing on relevant systems.
- Physical Examination: Checks for any visible signs of HAVS or related conditions.
2) Tier 2: Annual Screening Questionnaire
Purpose: Ongoing monitoring for all employees exposed to vibration at or above the action value.
Components:
- Questionnaire: On an annual basis to track symptoms like tingling, numbness, and loss of strength.
- Review: A competent person conducts this to identify any new symptoms or worsening conditions.
3) Tier 3: Clinical Assessment
Purpose: Detailed assessment for employees reporting symptoms or showing positive findings from Tier 2.
Components:
- Detailed Questionnaire: In-depth questions about the nature and severity of symptoms.
- Clinical Examination: A qualified occupational health professional provides this.
- Functional Tests: Assess grip strength, dexterity, and other capabilities.
4) Tier 4: Specialist Referral
Purpose: For cases requiring a specialist opinion or advanced diagnostic tests.
Components:
- Referral: To a specialist in occupational health or a relevant medical field.
- Advanced Diagnostic Tests: May include nerve conduction studies and other assessments.
By following this tiered approach, employers can effectively monitor and manage the health of their workers, ensuring early detection and treatment of HAVS, and maintaining a safer work environment.
Healthscreen’s HAVS Services
At Healthscreen, we provide a structured health surveillance program, adhering to the tier system for HAVS monitoring. Our services include:
- Tier 1: Initial Health Assessment: Establishes a baseline for new employees exposed to hand-arm vibration.
- Tier 2: Annual Screening Questionnaire: Ongoing monitoring through annual questionnaires to track symptoms.
- Tier 3: Clinical Assessment: Detailed assessment for employees reporting symptoms or showing positive findings from Tier 2.
If an employee requires further assessment, we can provide referrals to specialists for advanced diagnostic tests and treatment.
How to Get Started
Protecting your workers from HAVS starts with a proactive approach. To learn more about our services or to schedule an assessment, contact Healthscreen today. Our team is ready to assist you in implementing effective HAVS prevention and management strategies. Click the button below to get in touch with us and take the first step towards a safer workplace.